Prestressed concrete is a revolutionary technique that has transformed the construction industry, enabling the creation of stronger, more durable, and more efficient structures. This comprehensive guide will delve into the world of prestressed concrete, exploring its fundamental principles, advantages, applications, design considerations, manufacturing processes, and its significant role in shaping modern infrastructure.
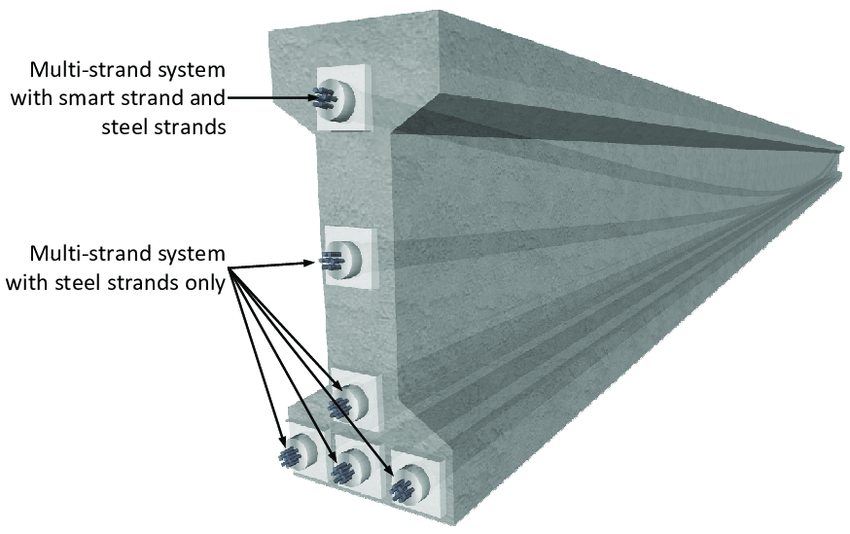
What is Prestressed Concrete? A Definition
Prestressed concrete is a structural material where internal compressive stresses are intentionally introduced to counteract tensile stresses resulting from applied loads. This pre-compression significantly enhances the concrete’s ability to resist cracking and improves its overall structural performance. In essence, it’s like putting concrete in a constant state of being squeezed together, making it much stronger and more resistant to bending and breaking.
Understanding the Underlying Principles:
Concrete is strong in compression (being squeezed) but weak in tension (being pulled apart). Traditional reinforced concrete relies on steel reinforcement to resist tensile forces. However, cracks can still form in the concrete, leading to potential durability issues and requiring thicker sections. Prestressed concrete addresses this limitation by introducing compressive forces before loads are applied, effectively neutralizing tensile stresses.
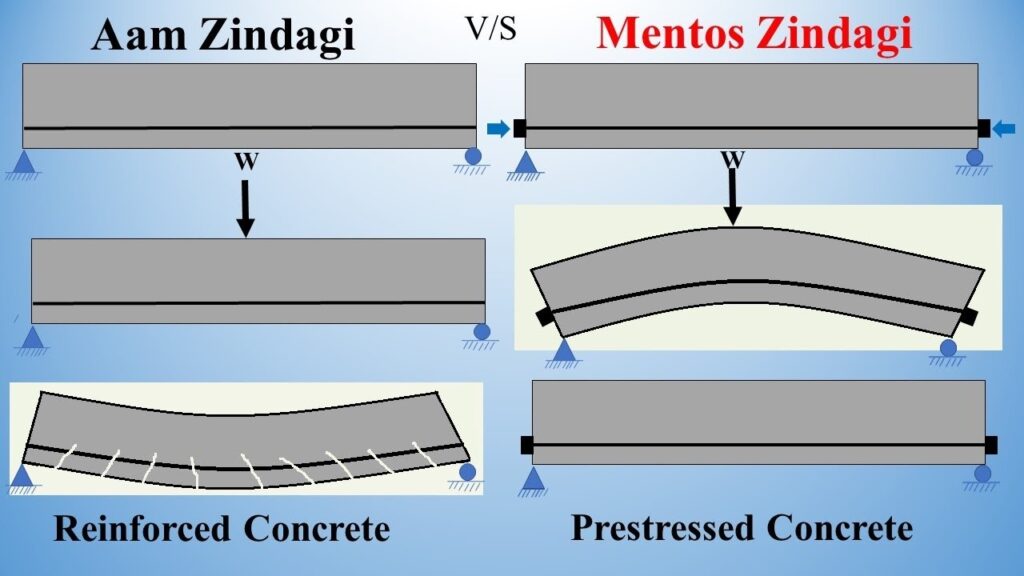
This leads to:
- Increased Load-Bearing Capacity: Structures can handle significantly heavier loads.
- Longer Spans: Bridges and buildings can span greater distances without intermediate supports.
- Reduced Deflection: Structures are less prone to bending or sagging under load.
- Improved Durability: Cracking is minimized, protecting the steel reinforcement from corrosion and extending the lifespan of the structure.
Two Primary Methods of Prestressed Concrete:
There are two main methods of creating prestressed concrete, each with its unique characteristics and applications:
- Pre-tensioned Concrete: In pre-tensioning, high-strength steel tendons are tensioned before the concrete is poured. These tendons are stretched between anchors on a casting bed. Concrete is then poured around the tensioned tendons and allowed to harden. Once the concrete has gained sufficient strength, the tendons are released, transferring the pre-stress force to the concrete through bond.
- Key Features of Pre-tensioning:
- Suitable for mass production of standardized elements.
- Requires specialized casting beds and equipment.
- Tendons are typically straight.
- Bond between tendons and concrete is crucial for stress transfer.
- Commonly used for precast concrete elements like bridge girders, hollow core slabs, and railway sleepers.
- SEO Keyword: Pre-tensioned concrete manufacturing
- Key Features of Pre-tensioning:
- Post-tensioned Concrete: In post-tensioning, ducts or sleeves are placed within the concrete formwork before the concrete is poured. After the concrete has hardened, high-strength steel tendons (cables or bars) are threaded through these ducts. The tendons are then tensioned using hydraulic jacks and anchored to the concrete at the ends of the member. This tensioning process applies compression to the concrete. Finally, the ducts are typically filled with grout to protect the tendons from corrosion and bond them to the concrete.
- Key Features of Post-tensioning:
- Suitable for both precast and cast-in-place construction.
- Allows for curved or draped tendons, optimizing stress distribution.
- Anchorage systems are critical for transferring the pre-stress force.
- Grouting provides corrosion protection and enhances bond.
- Commonly used for bridges, slabs-on-grade, high-rise buildings, and tanks.
- SEO Keyword: Post-tensioned concrete construction
- Key Features of Post-tensioning:
Why Choose Prestressed Concrete? Unveiling the Advantages
Prestressed concrete offers a wealth of benefits compared to traditional reinforced concrete and other construction materials. Here’s a detailed look at the key advantages:
- Increased Load-Carrying Capacity: This is a primary advantage. Prestressed concrete members can support significantly heavier loads than similarly sized reinforced concrete members. This is crucial for bridges, parking garages, and high-rise buildings.
- Longer Spans: Prestressed concrete enables the construction of longer spans with fewer intermediate supports. This creates more open and flexible interior spaces in buildings and reduces the number of piers required for bridges, lowering construction costs and improving aesthetics.
- Reduced Deflection: Prestressed concrete structures exhibit less deflection (bending) under load. This improves the structural integrity and appearance of the building and reduces the risk of cracking in finishes or other elements.
- Improved Durability: By minimizing cracking, prestressing protects the steel reinforcement from corrosion. This significantly extends the lifespan of the structure, reducing maintenance costs and enhancing its long-term performance.
- Reduced Concrete Volume: Prestressed concrete allows for the use of smaller and lighter structural members. This reduces the overall volume of concrete required, leading to material savings and lower construction costs.
- Cost-Effectiveness: While the initial cost of materials and specialized labor may be slightly higher, the long-term cost savings associated with reduced maintenance, increased lifespan, and optimized material usage often make prestressed concrete a more cost-effective solution.
- Enhanced Fire Resistance: Properly designed prestressed concrete structures can exhibit excellent fire resistance. The pre-compression helps to prevent cracking under thermal stress, maintaining the structural integrity of the member.
- Faster Construction: Precast prestressed concrete elements can be manufactured off-site and erected quickly, reducing construction time and minimizing disruption. This is particularly beneficial for infrastructure projects.
- Design Flexibility: Prestressed concrete offers considerable design flexibility. It can be used to create complex shapes and geometries, allowing architects and engineers to realize their creative visions.
- Reduced Maintenance: The durability and resistance to cracking of prestressed concrete structures minimize the need for maintenance and repairs, reducing long-term operating costs.
Applications of Prestressed Concrete: A Wide Range of Structures
The unique properties of prestressed concrete make it suitable for a wide array of applications in both buildings and infrastructure:
- Bridges: Prestressed concrete is extensively used in bridge construction for both short and long spans. It allows for lighter, more durable bridge decks and reduces the need for frequent maintenance.
- High-Rise Buildings: Prestressed concrete slabs and beams can provide longer spans, reduce column spacing, and increase floor-to-floor heights in high-rise buildings, maximizing usable space and improving architectural flexibility.
- Parking Garages: Prestressed concrete is ideal for parking garages due to its ability to resist heavy loads, withstand exposure to de-icing salts, and minimize cracking, reducing maintenance costs.
- Slabs-on-Grade: Post-tensioned slabs-on-grade are commonly used in commercial and industrial buildings to control cracking, reduce joint spacing, and provide a more durable and level surface.
- Tanks and Silos: Prestressed concrete is used to construct circular tanks and silos for storing liquids and granular materials. The pre-compression helps to resist tensile stresses caused by the internal pressure, preventing cracking and leakage.
- Nuclear Containment Structures: Prestressed concrete is used in the construction of nuclear containment structures due to its high strength, durability, and ability to resist seismic forces and radiation.
- Stadiums and Arenas: Prestressed concrete is used to create large, column-free spaces in stadiums and arenas, providing unobstructed views and enhancing the spectator experience.
- Marine Structures: Prestressed concrete is used in the construction of marine structures such as piers, docks, and seawalls due to its resistance to corrosion and harsh marine environments.
- Railway Sleepers: Pre-tensioned concrete sleepers are used extensively in railway tracks due to their durability, resistance to wear, and ability to maintain track alignment.
- Precast Concrete Elements: Prestressed concrete is widely used in the manufacture of precast concrete elements such as beams, columns, slabs, and wall panels, which can be quickly assembled on site, accelerating construction.
Design Considerations for Prestressed Concrete: A Deep Dive
Designing with prestressed concrete requires a thorough understanding of its unique structural behavior and the various factors that influence its performance. Here are some key design considerations:
- Pre-stressing Force: Determining the optimal pre-stressing force is crucial for achieving the desired structural performance. The pre-stressing force must be sufficient to counteract tensile stresses under load but not so high as to cause excessive compressive stresses.
- Tendon Layout: The layout of the tendons should be carefully designed to optimize stress distribution and minimize stress concentrations. Curved or draped tendons can be used to improve the efficiency of the pre-stressing force.
- Anchorage Design: The anchorage system is critical for transferring the pre-stressing force from the tendons to the concrete. The anchorage must be strong enough to resist the high tensile forces in the tendons and prevent slippage.
- Concrete Mix Design: The concrete mix should be carefully designed to achieve high strength, low shrinkage, and good durability. The mix should also be compatible with the pre-stressing system.
- Creep and Shrinkage: Creep (time-dependent deformation under sustained load) and shrinkage (volume reduction due to moisture loss) can significantly affect the long-term performance of prestressed concrete structures. These effects must be considered in the design.
- Loss of Pre-stress: Over time, the pre-stressing force can be reduced due to various factors such as elastic shortening of the concrete, creep, shrinkage, steel relaxation, and friction losses. These losses must be estimated and accounted for in the design.
- Shear Design: The shear capacity of prestressed concrete members should be carefully evaluated. Shear reinforcement may be required to resist shear forces, particularly near supports.
- Fire Resistance Design: The fire resistance of prestressed concrete structures should be determined based on the applicable building codes. The concrete cover over the tendons and the type of concrete used can significantly affect the fire resistance.
- Durability Considerations: Prestressed concrete structures should be designed to resist deterioration caused by environmental factors such as corrosion, freeze-thaw cycles, and chemical attack. Proper detailing, material selection, and construction practices are essential for ensuring durability.
- Code Compliance: The design should comply with all applicable building codes and standards. Local regulations may vary, so it is important to consult with local authorities and obtain the necessary permits.
- Seismic Design: When used in seismic regions, prestressed concrete structures require special design considerations to ensure they can withstand earthquake forces. Ductile detailing and robust connections are essential.
The Manufacturing Process: Ensuring Quality and Precision
The manufacturing process for prestressed concrete is crucial for ensuring the quality and performance of the final product. Here’s an overview of the key steps:
- Design and Detailing: The process begins with detailed design and engineering calculations to determine the optimal pre-stressing force, tendon layout, and reinforcement requirements.
- Tendon Preparation: High-strength steel tendons are carefully inspected and cut to the required length. For post-tensioning, tendons are often pre-assembled with anchors and placed in ducts.
- Formwork Construction: Formwork is constructed to the precise dimensions and shape of the desired concrete element.
- Tendon Placement: The tendons are carefully placed within the formwork according to the design specifications. For pre-tensioning, the tendons are tensioned before the concrete is poured. For post-tensioning, the tendons are placed in ducts.
- Concrete Pouring: High-quality concrete is carefully poured into the formwork and vibrated to consolidate the concrete and remove air pockets.
- Curing: The concrete is cured under controlled conditions to achieve the desired strength and durability.
- Tensioning (Post-tensioning only): After the concrete has hardened, the tendons are tensioned using hydraulic jacks and anchored to the concrete.
- Grouting (Post-tensioning only): The ducts are filled with grout to protect the tendons from corrosion and bond them to the concrete.
- Demolding: The hardened concrete element is carefully removed from the formwork.
- Inspection and Testing: The prestressed concrete element is inspected for any defects and tested to ensure it meets the design requirements.
Quality Control: A Cornerstone of Prestressed Concrete Construction
Stringent quality control measures are essential throughout the entire process of designing, manufacturing, and constructing prestressed concrete structures. This includes:
- Material Testing: Testing the strength and properties of the concrete and steel tendons.
- Dimensional Control: Ensuring that the formwork and finished elements are accurate to the specified dimensions.
- Tensioning Procedures: Verifying that the tendons are tensioned to the correct force and that the anchorage systems are properly installed.
- Grouting Procedures: Ensuring that the grout is properly mixed and injected into the ducts to provide complete corrosion protection.
- Non-Destructive Testing: Using non-destructive testing methods such as ultrasonic testing to detect any internal defects in the concrete.
Prestressed Concrete vs. Reinforced Concrete: A Comparison
While both reinforced concrete and prestressed concrete use steel and concrete to create strong structures, they differ significantly in their behavior and applications:
Feature | Reinforced Concrete | Prestressed Concrete |
Tensile Resistance | Steel reinforcement resists tensile forces after cracking | Pre-compression minimizes cracking, steel resists remaining tension |
Span Length | Typically shorter spans | Longer spans possible |
Deflection | Higher deflection under load | Lower deflection under load |
Durability | Susceptible to cracking and corrosion | Improved durability due to minimized cracking |
Material Usage | Higher concrete volume often required | Reduced concrete volume possible |
Cost | Generally lower initial cost | Potentially lower lifecycle cost due to durability |
Conclusion: Prestressed Concrete – A Sustainable and Innovative Solution
Prestressed concrete is a versatile and innovative construction material that offers numerous advantages over traditional methods. Its ability to create stronger, more durable, and more efficient structures makes it a valuable asset in modern construction. As the demand for sustainable and resilient infrastructure continues to grow, prestressed concrete is poised to play an increasingly important role in shaping the built environment. By embracing this technology, engineers and architects can create structures that are not only aesthetically pleasing but also structurally sound and environmentally responsible.
Call to Action:
- Consult with a Prestressed Concrete Specialist: Consult with an experienced structural engineer specializing in prestressed concrete design to assess its suitability for your project.
- Explore Industry Resources: Utilize resources from organizations like the Post-Tensioning Institute (PTI) and the Precast/Prestressed Concrete Institute (PCI) to learn more about prestressed concrete technology and best practices.
- Review Case Studies: Examine case studies of successful prestressed concrete projects to gain insights and inspiration.
By taking these steps, you can leverage the benefits of prestressed concrete to create high-performing, durable, and sustainable structures that meet the challenges of the 21st century.